テスラは「サイバーキャブをアンボックスプロセスで生産する」とサンディームンロのYouTubeチャンネルで初めて公表しました。
「アンボックスプロセス」は、自動車製造における革新的な手法で従来の直線的な組み立てラインを根本的に見直し、効率性、コスト削減、柔軟性を追求するものです。
従来の方法では、車両がコンベアベルト上を移動しながら各ステーションで部品が順次取り付けられていましたが、アンボックスプロセスでは、車両の各部分(ドアパネル、トランクなど)を独立したサブアセンブリとして別のエリアで色付け、組み立てされ、その後これらの大きなサブアセンブリが最後に集められ、一気に車両として統合されます。
テスラの車両開発副社長ラース・モラヴィは「我々は大型のリアキャスティングとフロントキャスティングを製造し、ホットスタンプ技術で成形した2つのドアリング(ドア以外の側面)で車両の側面を構成します。これらをレーザー溶接で接合し、内装やモーターなどの部品を組み込んだ後、ボルトで固定します」と説明。
また、外装パネルには「反応射出成形(RIM)」が採用されており、プラスチック素材(PPA、TPO、PC/ABS)にポリウレタンを注入し、ガラスやカーボンで強化した部品に超音波で接合。この手法は軽量で耐久性のあるパーツを生み出すと同時に、生産工程を簡素化します。
「複数の技術を組み合わせていますが、基本理念は『一度で完璧な部品を作る』こと。後処理や再調整を最小限に抑えたいのです」とラースは強調。これは、部品を作った後に何度も修正する手間を省き、時間とコストを削減する狙いがあります。
「外装は塗装しない。ホットスタンプ製のドアリング部分にボロン鋼の保護のために少し黒を塗るだけ。」
ムンロは「パネル成形時に色を直接練り込むのは大賛成。期待通りいけば、ホットケーキのように売れていくだろう」と語りました。
Attachments:
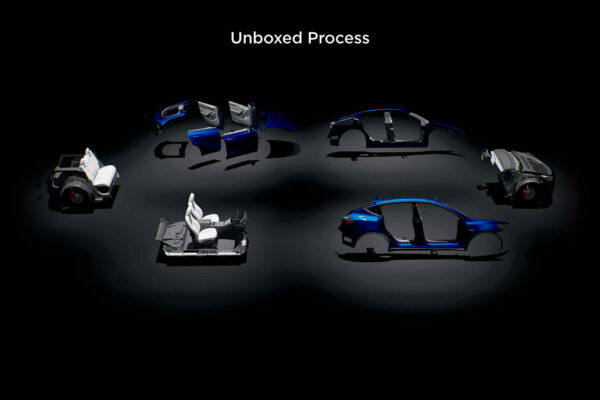